Part Manufacturing
Part manufacturing is one of the most critical sectors of industry, encompassing metal and plastic production services like simple welding, manifolds, and pipe assemblies. With its direct impact on the quality and performance of final products, part manufacturing has become a vital link in the production chain. At Farafan Tous Company, by combining engineering expertise, advanced equipment, and high-quality raw materials, we produce precise and high-durability parts for various industries. Our expertise lies in mold making and part manufacturing tailored to your specific needs!
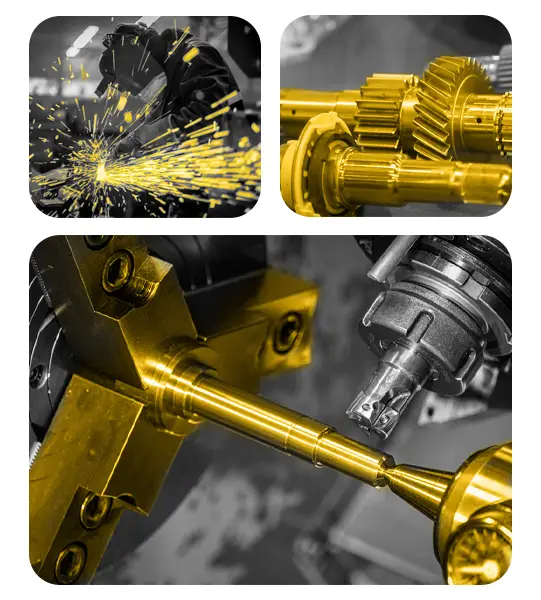
Frequently Asked Questions
\Yes, we have the capability to produce custom parts, and all stages from design to manufacturing are carried out based on the customer's needs.
The materials used include various metals such as steel and aluminum, polymers, and composites, which are selected based on the specific application.
Yes, we have the capacity for high-volume mass production of parts, as well as production in smaller scales.
All manufactured parts undergo quality control processes including dimensional testing, durability, and strength testing to ensure they meet customer standards.
Part Manufacturing: From the Potter’s Wheel to 3D Printers
Imagine you are driving your favorite car, or enjoying your latest smartphone model, or even watching a giant airplane fly. Have you ever wondered how many small and large parts, crafted with utmost precision and intricacy, are assembled to bring these amazing products to your hands?
This is where part manufacturing comes in! Part manufacturing is the art and science of creating various components with high precision and quality. These parts can be made from different materials such as metal, plastic, ceramic, and more, and are used in a wide range of industries.
We, at Farafan Tous Knowledge-Based Company, as one of the key players in this industry, are proud to play a role behind the scenes in the production of many high-quality Iranian products by providing specialized part manufacturing services. If you own a business that involves product manufacturing, you will likely require part manufacturing services. In this article, we will take a journey into the fascinating world of part manufacturing, exploring its history, methods, raw materials, applications, and future from Farafan Tous’s perspective. We will also examine key factors for choosing the best part manufacturing services. So, buckle up and join us!
But What Exactly is Part Manufacturing?
Simply put, part manufacturing means shaping raw materials (like metal, plastic, wood, etc.) to produce the required components for various industries. These parts can range from very simple (like a washer) to extremely complex (like an airplane turbine).
Why is Part Manufacturing So Important?
The importance of part manufacturing in today’s world is undeniable. Almost all products we interact with daily are comprised of various parts. From your smartphone and laptop to household appliances, medical equipment, and even the buildings we live in, all in some way rely on part manufacturing.
A Brief Journey Through the History of Part Manufacturing
You might think part manufacturing is a modern phenomenon, but it’s interesting to know that its roots go back thousands of years! Early humans made simple parts using stone and bone tools for hunting, building shelters, and making clothes. The potter’s wheel can be considered one of the first examples of part manufacturing.
With the passage of time and the advancement of civilizations, part manufacturing methods also evolved. In ancient times, metalworking and casting flourished, and skilled craftsmen were able to make more complex metal parts. The Industrial Revolution was a turning point in the history of part manufacturing. The invention of steam engines and later electric motors enabled the mass production of parts.
The advent of computers and automation in the 20th century created a great transformation in part manufacturing. CNC (Computer Numerical Control) machines, with high precision and speed, enabled the production of complex parts with very low tolerances. Today, advanced technologies like 3D printing, laser cutting, and electrical discharge machining have pushed the boundaries of part manufacturing.
The Diverse World of Part Manufacturing Methods
As mentioned, there are various methods for part manufacturing. Each of these methods has its own advantages, disadvantages, and specific applications. Let’s take a closer look at some of the most important of these methods.
Types of Part Manufacturing Methods: The Art of Choosing the Best Method (Farafan Tous Expertise)
Choosing the appropriate method for manufacturing a part depends on various factors such as the material, dimensions, required precision, production volume, etc. Here, we will mention some of the most common part manufacturing methods, and then we will also introduce Farafan Tous’s specific capabilities:
1. Traditional Methods:
Turning:
In this method, the workpiece rotates around its axis, and a cutting tool (single-point) removes material with linear movement. Turning is suitable for producing parts with cylindrical, conical, and screw shapes.
- Pros: High precision, good surface finish, ability to produce complex shapes.
- Cons: Limitation in part shape, requires operator skill.
- Applications: Crankshafts, shafts, bolts and nuts, automotive parts.
Milling:
In this method, a cutting tool (milling cutter) rotates around its axis, and the workpiece moves linearly or rotationally. Milling is suitable for creating flat surfaces, grooves, holes, and complex shapes in various parts.
- Pros: High variety in part shape, ability to produce complex parts, good precision.
- Cons: Slower speed compared to turning, requires more advanced machinery.
- Applications: Mold making, automotive parts, aerospace parts, electronic components.
Drilling:
Creating holes in parts using a drill bit.
- Pros: Simplicity, high speed.
- Cons: Limitation in hole diameter and depth, less precision than other methods.
- Applications: Creating holes for bolts and nuts, rivets, connections.
Grinding:
In this method, an abrasive wheel is used to remove a small amount of material from the part’s surface. Grinding is suitable for creating very smooth and precise surfaces, sharpening tools, and removing burrs (small protrusions).
- Pros: Very high precision, excellent surface finish.
- Cons: Slow speed, high cost.
- Applications: Toolmaking, precision parts, optical parts.
Sawing:
Cutting parts using manual or machine saws.
- Pros: Simplicity, high speed for straight cuts.
- Cons: Low precision, creates burrs, limitation in cut shape.
- Applications: Initial cutting of parts, cutting pipes and profiles.
Casting:
In this method, molten metal is poured into a mold of the desired shape, and after cooling, the part solidifies. Casting is suitable for producing complex parts in high volumes.
- Pros: Ability to produce complex parts, high volume, relatively low cost.
- Cons: Lower dimensional accuracy compared to machining methods, requires finishing operations.
- Applications: Automotive parts, engine parts, pump bodies.
Forging:
In this method, heated metal is subjected to pressure and impact to form the desired shape. Forging increases the part’s strength and toughness.
- Pros: High strength, good toughness, fatigue resistance.
- Cons: High cost, limitation in part shape.
- Applications: Crankshafts, connecting rods, gears, hand tools.
Injection Molding:
In this method, molten plastic is injected into a mold under pressure, and after cooling, the part solidifies. Injection molding is suitable for producing complex plastic parts in high volumes.
- Pros: Ability to produce complex parts, high volume, relatively low cost.
- Cons: Requires expensive molds, limitation in material selection.
- Applications: Plastic automotive parts, household appliances, toys, electronic components.
2. Advanced Methods:
CNC Machining:
This method uses Computer Numerical Control (CNC) machines for turning, milling, drilling, and other machining operations. CNC machines execute programmed instructions with high precision and speed, producing complex parts with very tight tolerances.
- Pros: Very high precision, repeatability, high speed, ability to produce complex parts.
- Cons: High initial cost, requires programming and skilled operators.
- Applications: Aerospace parts, medical parts, electronic components, mold making.
3D Printing (Additive Manufacturing):
In this method, the part is built layer by layer from various materials (plastic, metal, ceramic, etc.). A 3D printer uses a digital design file to deposit material in layers to form the final part.
- Pros: Ability to produce very complex parts, customization, rapid prototyping, reduced waste.
- Cons: Relatively high cost, limitation in material selection, lower strength compared to traditional methods.
- Applications: Rapid prototyping, production of customized parts, medical parts, aerospace parts.
Laser Cutting:
This method uses a laser beam to cut various materials (metal, plastic, wood, fabric, etc.). Laser cutting allows for precise and high-speed cutting of complex designs.
- Pros: High precision, high speed, ability to cut various materials, creates smooth edges.
- Cons: Relatively high cost, limitation in cutting thickness, creates heat in the cutting area.
- Applications: Cutting metal sheets, fabric cutting, engraving on wood and metal, making signs.
Plasma Cutting:
In this method, a hot plasma gas is used to cut conductive metals. Plasma cutting is suitable for cutting thick metal sheets.
- Pros: High speed, ability to cut thick sheets, lower cost compared to laser cutting.
- Cons: Lower precision compared to laser cutting, creates high heat, creates burrs.
- Applications: Cutting steel sheets, fabricating metal structures.
Electrical Discharge Machining (EDM):
This method uses controlled electrical sparks to remove material from the workpiece. EDM is suitable for producing complex parts with high precision in hard and conductive materials.
- Pros: Very high precision, ability to produce complex shapes in hard materials, no stress induced in the part.
- Cons: Slow speed, high cost, limitation in material selection.
- Applications: Mold making, manufacturing precision parts, producing medical parts.
Chemical Machining:
In this method, chemicals are used to remove material from the workpiece.
- Pros: No stress induced in the part, ability to machine thin parts.
- Cons: Relatively low machining precision, usually requires additional processes.
- Applications: Electronic parts production.
Electrochemical Machining (ECM):
In this method, an electric current and an electrolyte solution are used to remove material from the workpiece. ECM is suitable for producing complex parts with high precision in hard and conductive materials.
- Pros: No stress induced in the part, ability to produce complex shapes in hard materials, no tool wear.
- Cons: Slow speed, high cost, requires precise electrode design.
- Applications: Producing turbine blades, medical parts, aerospace parts.
Waterjet Cutting:
In this method, a very high-pressure water jet (sometimes with abrasive materials) is used to cut various materials (metal, plastic, stone, glass, etc.). Waterjet cutting is suitable for cutting heat-sensitive materials and creating complex designs.
- Pros: No heat generated, ability to cut various materials, no burrs created, environmentally friendly.
- Cons: Relatively high cost, slower speed than laser cutting, creates moisture.
- Applications: Cutting stone and ceramics, cutting glass, cutting automotive parts, cutting food materials.
Farafan Tous Special Capabilities:
In addition to the above methods, Farafan Tous Knowledge-Based Company, utilizing advanced equipment and the technical knowledge of its experts, also offers the following specialized services:
Stamping/Punching Presses:
At Farafan Tous, we have the capability to perform stamping with various tonnages, from 30 tons to 100 tons. This capability allows us to produce metal parts with diverse shapes and high precision. Furthermore, our 40-ton and 25-ton high-speed presses provide superb speed and precision in part production.
Deep Drawing Presses:
Equipped with powerful deep drawing presses, Farafan Tous is capable of performing deep drawing with tonnages from 30 tons to 600 tons. This capability allows us to produce deep and complex metal parts with excellent quality.
Spring Bending Presses:
For producing precise and high-quality springs, our specialized spring bending presses can process steel strips up to 1.25 mm thick and 31 mm wide.
Die Casting Presses:
With 400-ton and 250-ton die casting presses, Farafan Tous is capable of producing complex aluminum and Zamak parts in high volumes with unparalleled quality.
Injection Molding Machines:
For producing plastic parts, our 600-ton and 80-ton injection molding machines allow for the production of parts with various dimensions and complexities.
Raw Materials: From Hard Metals to Soft Plastics
Choosing the appropriate raw materials is one of the most important factors in part manufacturing. Different materials have different properties and are suitable for specific applications. Let’s take a look at some of the most common raw materials in part manufacturing:
Metals:
- Iron and Steel: High strength, good toughness, weldability, reasonable price. (Applications: automotive parts, metal structures, machinery)
- Aluminum: Lightweight, corrosion resistant, good machinability, high thermal and electrical conductivity. (Applications: aircraft bodies, automotive parts, household appliances)
- Copper: Very high thermal and electrical conductivity, corrosion resistant, good formability. (Applications: wires and cables, copper pipes, electronic components)
- Titanium: Very lightweight, very high strength, corrosion resistant, biocompatible. (Applications: aerospace parts, medical implants, surgical instruments)
Plastics:
- Thermoplastics: Can be melted and reshaped, lightweight, inexpensive. (Applications: plastic bottles, toys, household appliances)
- Thermosets: Do not melt after shaping, hard and resistant. (Applications: automotive parts, electrical components, adhesives)
- Composites: A combination of two or more materials with different properties.
- Carbon Fibers: Very lightweight, very high strength, fatigue resistant. (Applications: racing car bodies, aerospace parts, sports equipment)
- Fiberglass: Lightweight, corrosion resistant, inexpensive. (Applications: boat bodies, water tanks, automotive parts)
- Ceramics: Hard, heat and wear resistant, electrical insulator. (Applications: cutting tools, bearings, engine parts)
- Wood: Natural, beautiful, relatively inexpensive, good machinability. (Applications: furniture, cabinets, wooden structures)
Part Manufacturing Steps: From Idea to Final Product
The part manufacturing process typically includes the following steps:
Design (CAD):
In this step, the 3D design of the part is created using Computer-Aided Design (CAD) software. The designer must carefully determine the dimensions, tolerances, material type, and other part specifications. Design for Manufacturing (DFM) considerations must also be taken into account to ensure the part is manufacturable.
Planning (CAM):
In this step, the 3D design of the part is converted into codes understandable by machines (like CNC machines). CAM software determines the tool path, cutting speed, cutting depth, and other machining parameters. The machining process can also be simulated to ensure planning accuracy.
Manufacturing:
In this step, the part is manufactured using the appropriate part manufacturing method (turning, milling, 3D printing, etc.). Machines and tools must be accurately set up, and the operator must supervise the production process.
Finishing:
In this step, finishing operations like grinding, polishing, painting, coating, etc., are performed on the part to improve its appearance and properties.
Final Quality Control:
In this step, the part is examined for dimensions, tolerances, appearance, and functionality to ensure its compliance with design specifications.
Applications of Part Manufacturing: From Automotive to Aerospace, Medical to Electronics
As mentioned, part manufacturing has numerous applications in various industries, including:
- Automotive: Body, engine, chassis, suspension system, brakes, steering, interior parts.
- Aerospace: Aircraft body, jet engines, wings, satellite parts, rockets.
- Medical: Surgical instruments, implants, prosthetics, diagnostic equipment.
- Electronics: Printed Circuit Board (PCB), phone cases, computer parts, connectors.
- Architecture and Construction: Decorative metal and wood parts, prefabricated structures, doors and windows.
- Military Industries: Weapons, protective equipment, armored vehicles.
- Mold Making: Plastic injection molds, metal molds, casting molds.
- Food Industries: Packaging machinery, and food production.
- Oil and Gas Industry: Drilling equipment and machinery.
The Future of Part Manufacturing: Smarter, Faster, Greener
Part manufacturing is poised for significant advancements in the future:
Automation and Robotics:
The use of robots in production lines increases precision, speed, and safety, and reduces costs.
Artificial Intelligence (AI):
AI can optimize part manufacturing processes, predict defects, and improve quality.
3D Printing and Additive Manufacturing:
The production of complex and customized parts with high speed and low waste will become increasingly feasible.
Smart Materials:
Parts that can change their shape, color, or function in response to external stimuli will find new applications.
Nanotechnology:
The production of very small parts with improved properties will revolutionize various industries.
Sustainable and Environmentally Friendly Production:
Reducing energy consumption, using recycled materials, and reducing waste will gain more importance.
Choosing Part Manufacturing Services: Points to Consider
If you are looking for part manufacturing services, pay attention to the following points:
- Experience and Expertise: The service provider should have sufficient experience and expertise in part manufacturing.
- Equipment and Technology: Ensure the equipment and technologies used are up-to-date.
- Raw Material Quality: Be confident about the quality of the raw materials used.
- Precision and Tolerances: Check the achievable precision and tolerances.
- Delivery Time: Inquire about the lead time for parts.
- Cost: Compare the cost of services with other companies.
- After-Sales Service: Ensure after-sales service is available.
- Certifications and Standards: The company should have valid quality certifications and standards.
And Why Farafan Tous?
Knowledge-Based:
At Farafan Tous, relying on up-to-date technical knowledge and utilizing advanced technologies, we constantly strive to provide the best part manufacturing solutions to our customers.
Commitment to Quality:
Quality is our main priority at Farafan Tous. By using advanced equipment and precise process control, we guarantee that our manufactured parts meet the highest quality standards.
Customer-Centricity:
At Farafan Tous, we value the needs and desires of our customers and constantly strive to achieve their complete satisfaction by providing consulting services and technical support.
Advanced Equipment:
Farafan Tous’s investment in modern and up-to-date equipment guarantees quality and precision in part production. Some of our key equipment includes:
- Laser metal cutting up to 8 mm thickness
- Coil uncoiler and straightener
- Guillotine for sheet cutting up to 4 mm thickness
- Feeder
- Overhead crane with up to 11 tons capacity
Conclusion: Part Manufacturing, The Beating Heart of Industry (Farafan Tous is With You)
Part manufacturing is a vital and dynamic industry that plays an important role in the production of various types of products. From small and precise electronic parts to large and complex aerospace components, all come into existence thanks to the art and science of part manufacturing.
At Farafan Tous Knowledge-Based Company, we proudly announce that by providing specialized part manufacturing services, we are by your side to turn your ideas into reality. By choosing Farafan Tous, you can be assured of our quality, precision, and commitment.
Sources and References:
- Book “Fundamentals of Manufacturing Processes” by Groover
- Book “Machine Tool Technology”
- Websites of Specialized Part Manufacturing Associations
- Scientific and Specialized Articles in the Field of Part Manufacturing